Butterfly Valve Manufacturer
Only unexpected, nothing impossible
WHO IS BUTTERFLY VALVE ?
A butterfly valve is a type of flow control device used in pipelines to regulate or isolate fluid flow. It is named for its disc, which resembles a butterfly’s wings, and is a key component in many industrial and commercial fluid systems.
BUTTERFLY VALVE Series
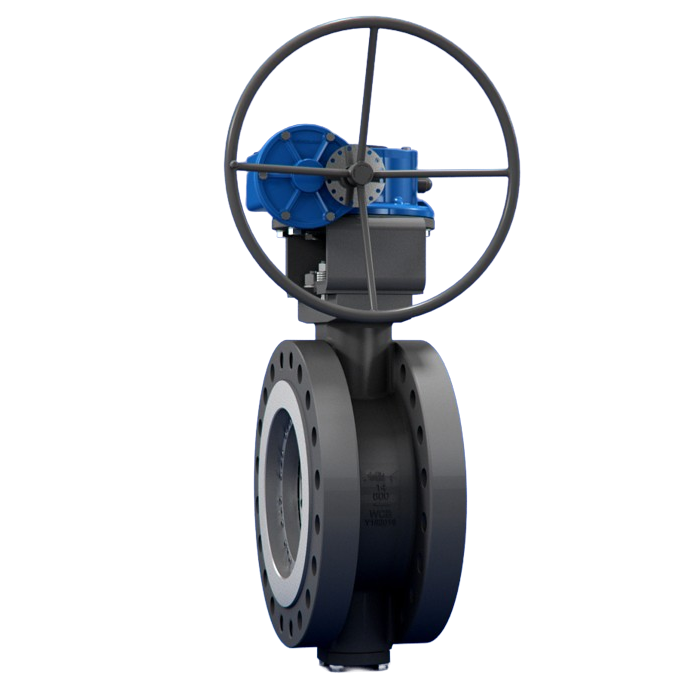
Triple Eccentric Butterfly Valve
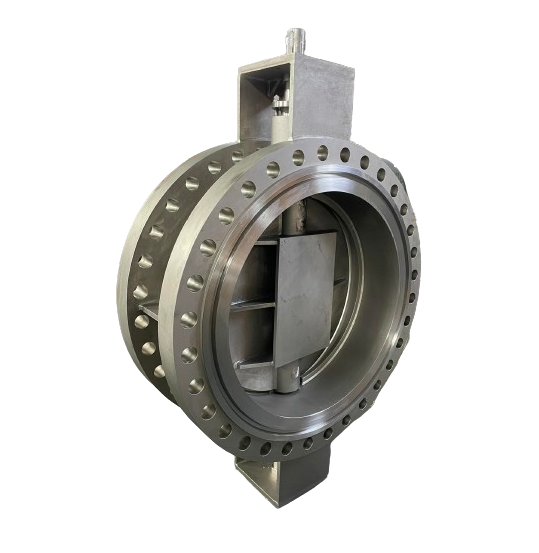
Double Eccentric Butterfly Valve
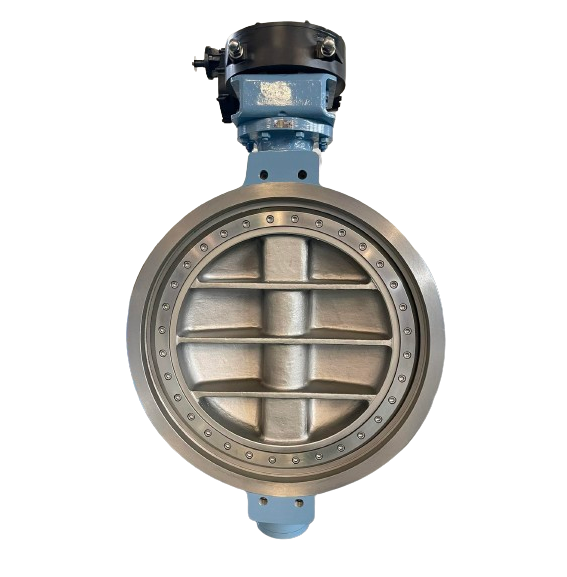
Wafer Butterfly Valve
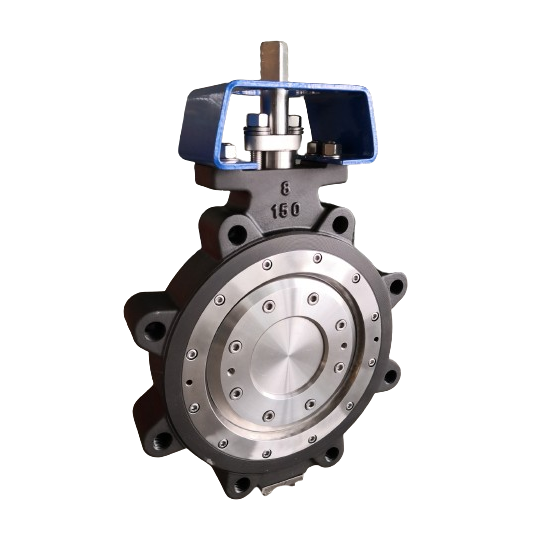
Lug Butterfly Valve

Metal Seal Butterfly Valve
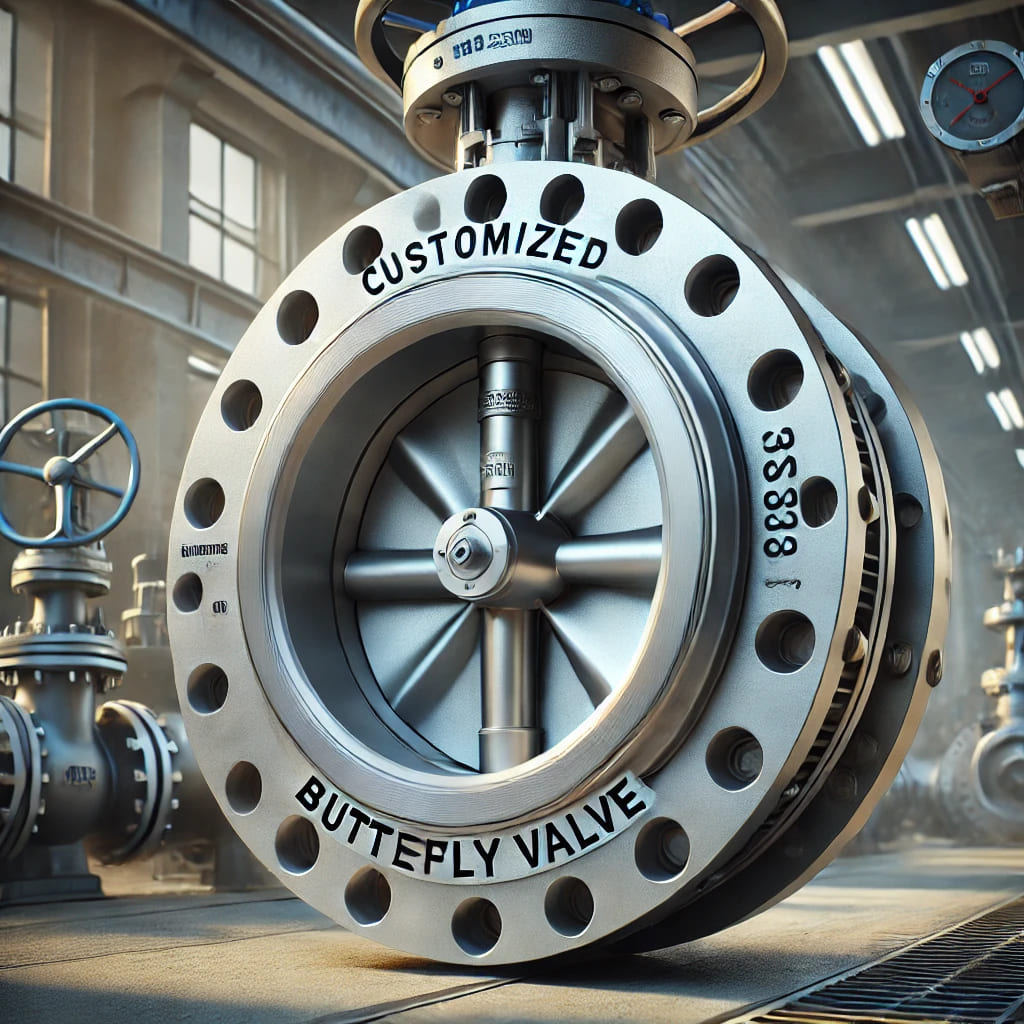
Customized your Butterfly Valve
How Does Butterfly Valve Work ?
A butterfly valve operates by using a central disc mounted on a shaft to control fluid flow through a pipeline. The disc, positioned in the middle of the valve body, rotates around the shaft, which is connected to an actuator or handle. When the valve is in the open position, the disc is aligned parallel to the flow of the fluid, allowing it to pass through the valve with minimal resistance.
To regulate flow, the disc can be partially rotated to restrict the passage, adjusting the flow rate according to the disc’s angle. When the valve is fully closed, the disc is rotated perpendicular to the flow, blocking the passage and creating a seal against the valve seat, which prevents fluid from leaking through.
Butterfly valves are known for their compact design, quick operation, and versatility, making them ideal for applications in water treatment, chemical processing, and HVAC systems.
Butterfly Valve Main Components:
- Body: The outer casing of the butterfly valve that holds all the internal components. It is typically made of materials like cast steel, cast iron, stainless steel…
- Seat: The sealing surface inside the valve body where the disc sits when the valve is closed. The seat ensures a tight seal to prevent leakage. It can be made of elastomers, such as rubber, or more durable materials like metal for high-temperature or high-pressure applications.
- Disc (Valve Plate): The rotating component inside the valve that controls the flow of fluid. When the disc is turned parallel to the flow, the valve is open; when turned perpendicular, the valve is closed. The disc can be made of metal, plastic, or a combination of materials.
- Shaft (Stem): A rod that connects the disc to the actuator or handle outside the valve body. The shaft allows the disc to rotate when the actuator or handle is turned. The shaft is usually made of stainless steel or another corrosion-resistant material.
- Bearings/Bushings: Components that support the shaft and ensure smooth rotation of the disc. They reduce friction and wear, enhancing the durability and operational efficiency of the valve.
- Actuator/Handle: The external mechanism that controls the position of the disc. It can be a manual handle, gear, or an automated actuator (pneumatic, electric, or hydraulic), allowing for remote operation and precise control of the valve.
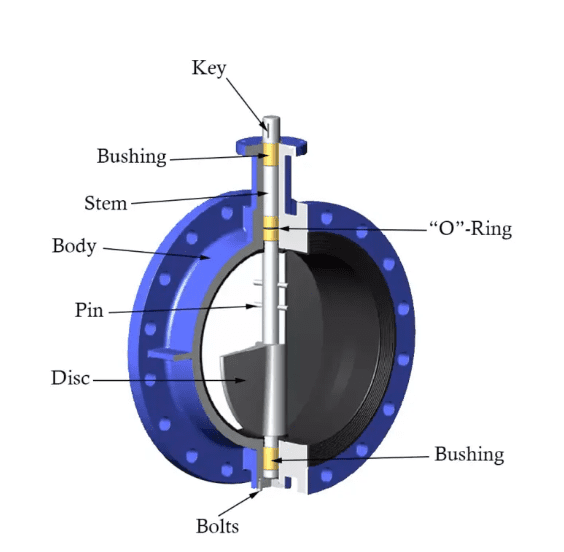
Why Choose Butterfly Valve?
Butterfly valves are known for their compact size and lightweight design, which makes them easier to install and requires less space compared to other types of valves like gate or globe valves. This feature is particularly beneficial in systems with space constraints.
Butterfly valves can be opened or closed quickly with a simple 90-degree turn of the actuator or handle. This rapid operation is ideal for applications where fast response times are critical, such as emergency shutdowns or automated systems.
Butterfly valves are generally more cost-effective than other types of valves, especially in larger sizes. Their simpler design means fewer components, which reduces manufacturing and maintenance costs.
When fully open, the disc of a butterfly valve presents minimal obstruction to flow, resulting in a low pressure drop across the valve. This helps maintain system efficiency and reduces energy consumption.
Butterfly valves provide reliable sealing with either soft seats for low-pressure applications or metal seats for high-temperature or high-pressure environments. This versatility in sealing options ensures leak-tight performance in various conditions.
The simple design of butterfly valves makes them easy to install and maintain. Many models allow for quick disassembly, facilitating cleaning, inspection, and replacement of parts without requiring extensive downtime.
Butterfly valves can be easily automated with pneumatic, electric, or hydraulic actuators, allowing for precise control and integration into complex automated systems. This is particularly useful in modern industrial processes that require high levels of control and monitoring.
With proper material selection and maintenance, butterfly valves offer a long service life, providing reliable performance over extended periods. Their durability makes them a cost-effective solution for long-term use.
Categorization of BUTTERFLY VALVE
By Design:
- Wafer-Type Butterfly Valve:
- This design is compact and lightweight, fitting between two pipe flanges. It is held in place by the tension of the flange bolts and does not have its own set of bolts, making it cost-effective but not suitable for applications requiring high-pressure resistance.
- Lug-Type Butterfly Valve:
- This type has threaded inserts (or “lugs”) around the valve body that allow it to be bolted directly to the flanges on either side. Lug-type valves can handle higher pressures and can be used in dead-end service (where one side of the valve is isolated).
- Flanged Butterfly Valve:
- Flanged butterfly valves have flanges integrated into the valve body, allowing them to be bolted directly to the pipeline. This design is robust and suitable for handling higher pressures and larger pipe diameters.
- Double Offset Butterfly Valve (High-Performance Butterfly Valve):
- The disc is slightly offset from the centerline of the valve seat and the body, reducing friction and wear. This design provides a tighter seal and is suitable for applications involving higher pressures and temperatures.
- Triple Offset Butterfly Valve:
- The disc is offset in three different ways, further reducing contact between the disc and seat during operation. This design provides a metal-to-metal seal, making it ideal for high-temperature, high-pressure, and critical applications.
- Wafer-Type Butterfly Valve:
By Sealing Mechanism:
- Soft-Seated Butterfly Valve:
- Features a resilient elastomer seat that provides a tight seal. It is typically used in low- to medium-pressure applications where chemical resistance is important.
- Metal-Seated Butterfly Valve:
- Uses a metal-to-metal seal, which is more durable and can handle higher temperatures and pressures. Ideal for industrial applications where soft seats would degrade
- Soft-Seated Butterfly Valve:
By Flow Control Characteristics::
On/Off Butterfly Valve:
- Designed primarily for fully open or fully closed positions, these valves provide simple, straightforward flow control without intermediate settings.
Throttling Butterfly Valve:
- Used for precise flow regulation, these valves can be adjusted to various positions between fully open and fully closed, providing fine control over the flow rate.
By Operation:
- Manual Butterfly Valve:
- Operated by a handwheel or lever, this type of butterfly valve is commonly used in applications where automation is not required, and manual control is sufficient.
- Pneumatic Butterfly Valve:
- Uses compressed air to operate the valve, allowing for quick and automated control. Pneumatic actuators are commonly used in industries where fast, repeated operations are necessary.
- Electric Butterfly Valve:
- Powered by an electric motor, this type allows for precise and automated control of the valve. It is suitable for remote operation and integration into complex control systems.
- Hydraulic Butterfly Valve:
- Operated by hydraulic fluid pressure, these valves are used in heavy-duty applications where strong and reliable force is required to move the valve.
- Manual Butterfly Valve:
By Material:
- Metallic Butterfly Valve:
- Constructed from metals like stainless steel, cast iron, or bronze, these valves are suitable for applications involving high pressures, temperatures, or corrosive fluids.
- Plastic Butterfly Valve:
- Made from materials like PVC, CPVC, or polypropylene, these valves are used in applications where corrosion resistance is critical, such as in chemical processing or water treatment.
- Lined Butterfly Valve:
- The interior surfaces of the valve are lined with a material like PTFE (Teflon) or rubber. Lined valves are used for handling aggressive chemicals or abrasive fluids.
- Metallic Butterfly Valve:
By Application:
- HVAC Butterfly Valve:
- Used in heating, ventilation, and air conditioning systems to control the flow of air or water. These valves are typically designed for low-pressure applications.
- Sanitary Butterfly Valve:
- Designed for use in food, beverage, and pharmaceutical industries, these valves are easy to clean and made from materials that meet strict hygiene standards.
- High-Pressure Butterfly Valve:
- Built to withstand high pressures, often used in oil and gas, power generation, and industrial processing applications.
- Cryogenic Butterfly Valve:
- Specifically designed to operate at extremely low temperatures, suitable for handling cryogenic fluids like liquid nitrogen or natural gas.
- HVAC Butterfly Valve:
Most Popular Questions for
BUTTERFLY VALVE
Leakage in a butterfly valve can be caused by several factors, including a worn or damaged seat, improper installation, or debris lodged between the disc and the seat. Regular inspection and maintenance, ensuring the correct installation, and keeping the pipeline clean can help prevent leakage. If leakage occurs, check the seat for wear and replace it if necessary.
A stuck disc can result from corrosion, debris buildup, or a misaligned shaft. To resolve this, inspect the valve for corrosion and clean any debris. Regular maintenance, including lubrication of the shaft and cleaning the valve, can prevent the disc from sticking. If corrosion is severe, the affected parts may need to be replaced.
Difficulty in operating a butterfly valve can be due to a tight fit between the disc and the seat, improper installation, or lack of lubrication. Ensure that the valve is correctly installed, and check for proper alignment. Applying appropriate lubrication to the shaft and bearings can make the operation smoother. If the issue persists, the actuator or handle may need to be adjusted or replaced.
To prevent wear on the valve seat, ensure that the valve is used within its specified pressure and temperature limits. Regularly inspect the seat for signs of wear and replace it if necessary. Using a valve with a compatible seat material for the specific fluid and operating conditions can also extend the seat’s lifespan.
A high-pressure drop across a butterfly valve may be caused by an oversized valve, excessive throttling, or an improperly sized disc. To minimize pressure drop, ensure that the valve is correctly sized for the application, and avoid excessive throttling by using the valve in its fully open or fully closed positions whenever possible.
Valve vibration can result from turbulent flow, cavitation, or improper installation. To reduce vibration, ensure that the valve is properly installed with adequate support and that the flow conditions are within the valve’s design limits. In some cases, using a valve with a different disc design or material may help mitigate vibration.
If the actuator is not functioning correctly, check the power supply, wiring, and connections. Ensure that the actuator is correctly sized for the valve and that it is properly aligned with the valve shaft. If the actuator is pneumatic or hydraulic, check for adequate air or fluid pressure. If the issue persists, the actuator may need repair or replacement.
To prevent corrosion, select a valve made from materials compatible with the fluid and operating environment. Regularly inspect the valve for signs of corrosion and address any issues promptly. In highly corrosive environments, consider using valves with corrosion-resistant coatings or made from special alloys like stainless steel or Hastelloy.
Signs that a butterfly valve may need replacement include persistent leakage, excessive wear on the seat or disc, difficulty in operation despite maintenance, and significant corrosion. If repairs are no longer cost-effective or the valve is no longer performing reliably, it may be time to replace it with a new one.
Ensuring long-term reliability involves regular maintenance, proper installation, and using the valve within its design specifications. Periodic inspection for wear, corrosion, and proper function is crucial. Using high-quality valves suited to the specific application and environment, combined with timely repairs or part replacements, will enhance reliability and extend the valve’s service life.
Customized your Valves with EASY!
Tell Us What You Need
Input the valve information you need, such as size, pressure, material and so on.
Directly upload datasheets or drawings.
Get Quote & Solution≤18h
To get a quote in less than 18 hours and have projects executed more easily and procurement streamlined, pls complete this form.
Get Drawing & Datasheet≤24h
For the normal valves, we can provide the drawings or datasheets wihtin 24 hours. For the customzied valves or large project, provide the drawings or datasheet within 48 hours.
Get A Fast Quote
Don’t let delays slow down your operations. Click here to fill out our quick quote form. And we’ll get back to you with a price and delivery time as soon as possible.