Check Valve Manufacturer
Only unexpected, nothing impossible
WHO IS CHECK VALVE ?
A check valve, also known as a non-return valve, is a type of valve that permits fluid to flow in one direction only, preventing backflow. It ensures that fluid flows in the desired direction in systems such as pipelines, pumps, and industrial processes. The valve operates automatically, with a disc or ball that moves to allow forward flow and seals to prevent reverse flow, maintaining system integrity and protecting equipment from potential damage caused by backflow.
CHECK VALVE Series
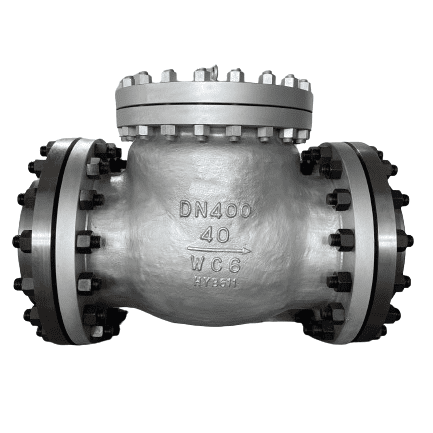
Cast Steel Check Valve
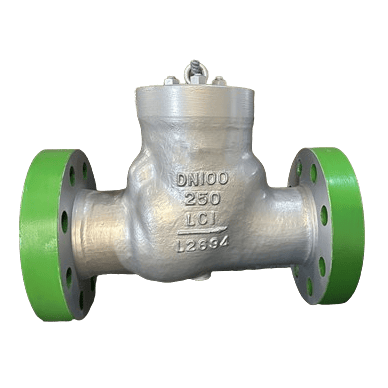
Pressure Seal Check Valve
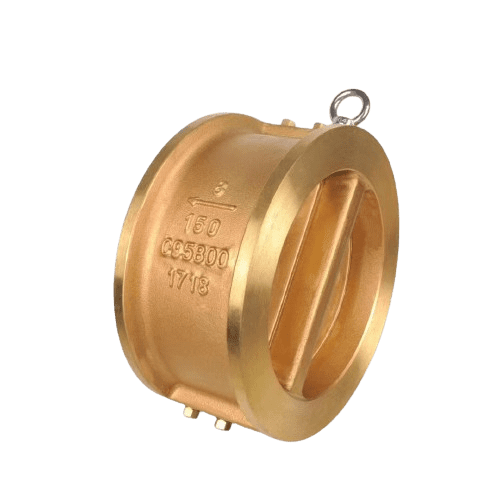
Wafer Check Valve
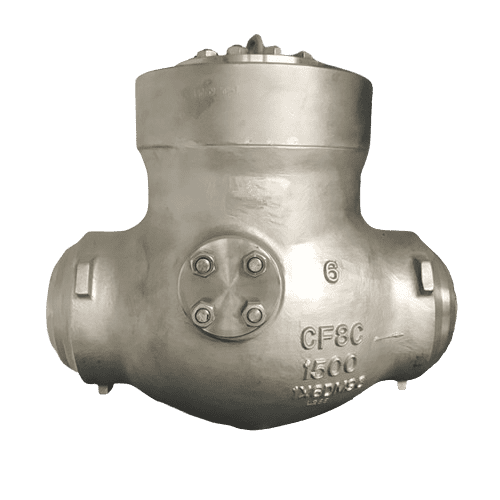
Tilting Disc Check Valve
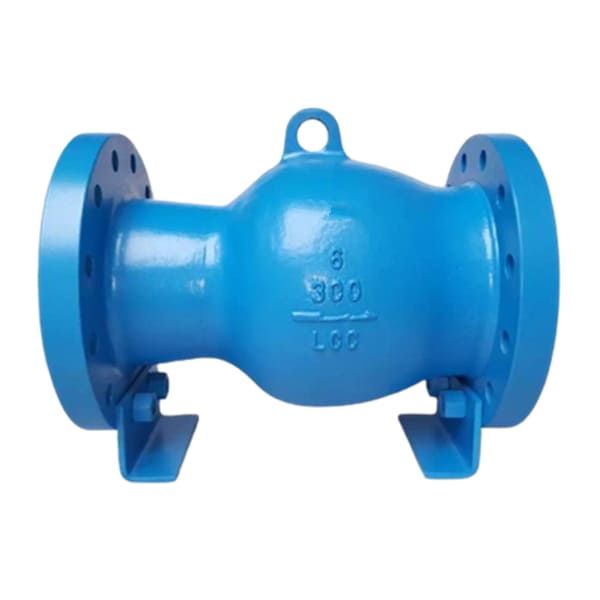
Axial Flow Check Valve
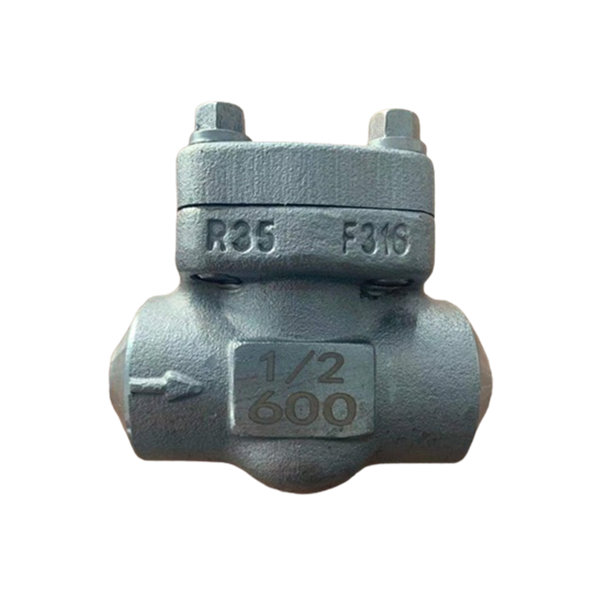
Forged Check Valve
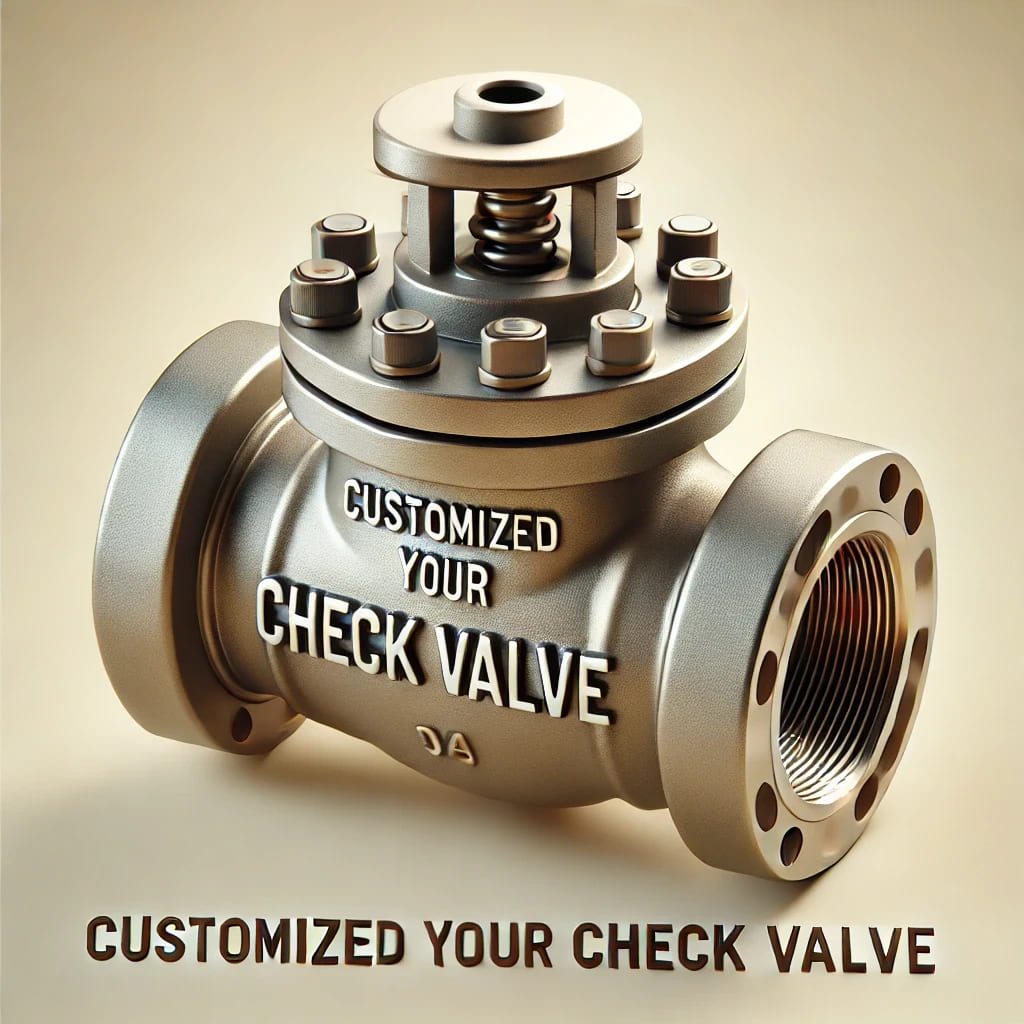
Customzie your Check Valve
How Does Check Valve Work ?
A check valve, also known as a non-return valve, operates by allowing fluid to flow in one direction only and preventing backflow. The main components of a check valve include the body, disc or poppet, seat, and sometimes a spring. When fluid flows in the desired direction, the pressure pushes the disc away from the seat, allowing the fluid to pass through. This is the open position of the valve.
When the fluid tries to reverse direction, the backflow pressure pushes the disc back against the seat, closing the valve. This prevents the fluid from flowing backward. In some designs, a spring is used to assist in closing the valve quickly and securely. The simplicity of its operation and automatic response to flow direction make the check valve essential in systems where backflow prevention is critical. They are widely used in various applications, including water and wastewater systems, oil and gas, chemical processing, and HVAC systems. Check valves help maintain system integrity, protect equipment, and ensure proper flow direction.
Check Valve Main Components:
- Body: The main structure that houses all the internal parts of the valve and provides connections to the pipeline.
- Seat: The surface against which the disc or poppet rests to form a seal, preventing backflow when the valve is closed.
- Disc: The movable part that opens to allow fluid flow in the forward direction and closes to prevent backflow. The shape and type of disc can vary, such as a ball, swing, or lift type.
- Spring (if applicable): In some check valve designs, a spring is used to help the disc or poppet return to the closed position quickly when forward flow stops.
- Hinge Pin (in swing check valves): In swing check valves, the hinge pin allows the disc to swing open and closed.
- Cover or Bonnet: The part that covers the internal components and can be removed for maintenance. It also provides access to the internals of the valve.
- Retainer (if applicable): Used in some designs to hold the disc or poppet in place and ensure proper alignment and operation.
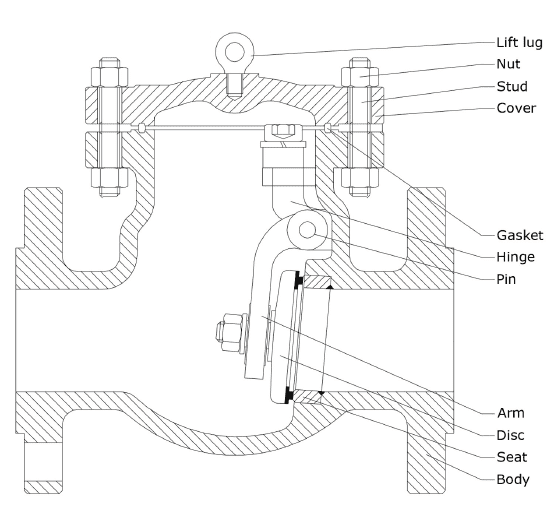
Why Choose Check Valve?
The main purpose of a check valve is to prevent backflow in the system. This ensures that the fluid flows in the desired direction and avoids contamination or damage to equipment.
Check valves protect sensitive components such as pumps, compressors, and pipelines from damage caused by reverse flow. By preventing backflow, check valves reduce the risk of equipment failure and minimize downtime for repairs and maintenance.
Check valves help maintain system pressure by preventing the reverse flow of fluid, ensuring efficient operation. By maintaining the correct flow direction, check valves contribute to energy savings by reducing the need for additional pumping or pressurization.
Check valves can be easily integrated with other types of valves, such as gate valves and globe valves, to enhance system functionality. They can be used in conjunction with other valves to create more complex and efficient fluid control systems.
Check valves automatically open and close based on the flow direction, requiring no manual intervention or external power. This automatic operation ensures consistent performance and reduces the likelihood of human error.
In some systems, check valves can act as a safeguard against overpressure conditions, protecting the system and equipment. In emergency scenarios, check valves can quickly close to prevent hazardous backflow, ensuring safety
Check valves are typically compact and require less installation space compared to other types of valves, making them ideal for systems with limited space. Their small footprint allows for easy integration into existing systems without major modifications.
Many check valves are designed to handle high flow rates without causing significant pressure drops. High flow capacity ensures efficient and effective fluid transfer, particularly in systems requiring large volumes.
Categorization of CHECK VALVE
By Mechanism of Action:
- Swing Check Valve: A disc swings on a hinge or shaft to allow flow in one direction.
- Lift Check Valve: The disc moves vertically to block or allow flow, suitable for horizontal or vertical piping.
- Ball Check Valve: Utilizes a ball to block or allow flow, moving in response to pressure changes.
- Disc Check Valve: Features a disc that moves axially against a spring to allow or block flow.
- Dual Plate Check Valve: Comprises two spring-loaded plates that fold back to allow flow and close to prevent backflow.
By Installation Orientation:
- Horizontal Check Valve:
- Description: Specifically designed for horizontal installation.
- Applications: Used in systems where horizontal flow control is required.
- Vertical Check Valve:
- Description: Designed for vertical installation, usually with upward flow.
- Applications: Ideal for sump pumps, vertical pipelines, and systems with limited horizontal space.
By Design and Structure:
- Wafer Check Valve: Thin, compact design that fits between flanges. Lightweight and space-saving.
- Flanged Check Valve: Features flanged ends for secure installation and easy removal.
- Threaded Check Valve: Features flanged ends for secure installation and easy removal.
- Inline Check Valve: Integrated within a pipeline, providing minimal disruption to flow.
By Material of Construction:
- Metallic Check Valve:
- Materials: Typically made from stainless steel, brass, or cast iron.
- Applications: Used in high-pressure, high-temperature, and corrosive environments.
- Non-Metallic Check Valve:
- Materials: Made from PVC, CPVC, or other plastic materials.
- Applications: Ideal for low-pressure and non-corrosive applications, such as water treatment and chemical handling.
By Special Function:
- Silent Check Valve:
- Description: Designed to close quietly, reducing water hammer and noise.
- Applications: Used in residential, commercial, and industrial systems where noise reduction is important.
- Spring-Loaded Check Valve:
- Description: Uses a spring to assist in closing the valve, ensuring quick response.
- Applications: Suitable for fast-flowing systems and high-cycle applications.
- Non-Slam Check Valve:
- Description: Prevents slamming shut by gradually closing, reducing shock and noise.
- Applications: Ideal for pump systems and applications prone to water hammer.
By Actuation Method:
- Gravity Check Valve: Relies on gravity to close the valve when the flow stops.
- Hydraulic Check Valve:Uses hydraulic pressure to assist in closing the valve.
- Pneumatic Check Valve:Uses air pressure to control the valve’s operation.
By End Connection Type:
- Flanged Check Valve: Features flanged ends that bolt directly to mating flanges on the pipe.
- Threaded Check Valve: Comes with threaded ends that screw into threaded pipe fittings.
- Socket Weld Check Valve: Has ends designed to be socket welded to the piping system.
- Butt Weld Check Valve: Features ends that are butt welded to the pipes for a seamless connection.
- Lug Check Valve: Similar to wafer check valves but includes lugs for secure bolting to the piping system.
- Grooved End Check Valve: Has grooved ends that are connected to the piping system using couplings.
- Compression Check Valve: Equipped with compression fittings that connect to pipes without threading or welding.
- Clamp Check Valve: Features clamp ends that use a clamping mechanism to connect to the piping system.
Most Popular Questions for
CHECK VALVE
- Description: The check valve fails to prevent the reverse flow of fluid.
- Cause: Debris blocking the valve, worn-out components, or incorrect installation.
- Solution:
- Inspection: Regularly inspect the valve for debris and clean as necessary.
- Replacement: Replace worn or damaged components.
- Installation Check: Ensure the valve is installed correctly according to the flow direction indicated.
- Description: A shock wave occurs when the flow of fluid is suddenly stopped, causing noise and potential damage.
- Cause: Rapid closure of the valve, high flow velocity.
- Solution:
- Valve Selection: Use silent or non-slam check valves designed to mitigate water hammer.
- Flow Control: Reduce flow velocity by adjusting the system design or using flow restrictors.
- Description: The valve disc or ball gets stuck, preventing proper operation.
- Cause: Accumulation of debris, corrosion, or improper lubrication.
- Solution:
- Cleaning: Regularly clean the valve to remove any debris.
- Material Selection: Use valves made of corrosion-resistant materials for corrosive environments.
- Lubrication: Ensure proper lubrication of moving parts as required.
- Description: Fluid leaks through the valve even when it is closed.
- Cause: Worn-out seals, damaged seating surfaces, or improper closing of the valve.
- Solution:
- Seal Replacement: Regularly inspect and replace worn seals.
- Seating Surface Repair: Repair or replace damaged seating surfaces.
- Proper Operation: Ensure the valve is properly installed and operated within its design parameters.
- Description: Excessive pressure drop across the valve reduces system efficiency.
- Cause: Valve design not suitable for the application, flow restriction by debris.
- Solution:
- Valve Selection: Choose a check valve designed for low pressure drop applications.
- Maintenance: Regularly clean the valve to prevent flow restriction.
- Description: The valve produces noise during operation, often due to water hammer or turbulence.
- Cause: Rapid closure of the valve, high flow velocity, or turbulence.
- Solution:
- Silent Check Valve: Use a silent check valve to reduce noise.
- Flow Control: Lower the flow velocity and ensure smooth flow paths in the system.
- Description: Over time, the valve components wear out, affecting performance.
- Cause: Continuous operation under harsh conditions, improper maintenance.
- Solution:
- Regular Maintenance: Perform regular maintenance checks and replace worn components as needed.
- Material Selection: Use durable materials suited for the specific application conditions.
- Description: The chosen check valve is not suitable for the application, leading to operational issues.
- Cause: Inadequate consideration of application requirements.
- Solution:
- Application Review: Thoroughly review the application requirements including pressure, temperature, fluid type, and flow rate.
- Expert Consultation: Consult with valve experts or manufacturers to select the appropriate valve type.
- Description: The valve seat is damaged, leading to poor sealing and leakage.
- Cause: Abrasive particles, improper closing, or frequent cycling.
- Solution:
- Regular Inspection: Inspect the valve seat regularly and repair or replace it as needed.
- Proper Handling: Ensure proper operation to prevent slamming and frequent cycling.
- Filtration: Use filters to remove abrasive particles from the fluid.
- Description: Debris or foreign particles in the piping system can prevent the valve from operating correctly.
- Cause: Inadequate cleaning of the piping system before installation.
- Solution:
- Clean Piping: Thoroughly clean the piping system before installing the check valve to remove any debris or foreign particles.
Customized your Valves with EASY!
Tell Us What You Need
Input the valve information you need, such as size, pressure, material and so on.
Directly upload datasheets or drawings.
Get Quote & Solution≤18h
To get a quote in less than 18 hours and have projects executed more easily and procurement streamlined, pls complete this form.
Get Drawing & Datasheet≤24h
For the normal valves, we can provide the drawings or datasheets wihtin 24 hours. For the customzied valves or large project, provide the drawings or datasheet within 48 hours.
Get A Fast Quote
Don’t let delays slow down your operations. Click here to fill out our quick quote form. And we’ll get back to you with a price and delivery time as soon as possible.